- Sitemap
- |
- Download
- |
- Blog
- |
- Contact Us
- |
- Inquiry List
Categories
Contacts Info.
Escalator Drive Chain
Description
Shopping Guide
Selection of chain drive power
Maintenance for roller chain drive
PRODUCT CENTER
JIEFENG GROUP, founded in 2007, is a global elevator and escalator parts manufacturer.We have our elevator guide rail factory, direct holding escalator step chain factory, own elevator, and escalator parts company.
In the Product Center, a wide range of JIEFENG's product lines can be found: Elevator machined guide rail, Elevator hollow guide rail, Elevator cold drawn guide rail, Elevator guide rail fish plate, Escalator step chain, Traction machine, elevator and escalator spare parts, etc.
Escalator step chains![]() |
Escalator drive chains![]() |
Escalator drive chains
● Escalator drive chain is divided into main drive chain and handrail belt drive chain, which are designed according to ISO 606 standards, and its interchangeability dimension is consistent with standard roller chains, mainly A series, B series roller chains, and its reinforced chain.
● Using high-quality materials and advanced processing technology, the product has the characteristics of high tensile strength and high fatigue strength; The tensile strength of the reinforced main drive chain reaches 1.2 times the minimum tensile strength of ISO standard, and the fatigue strength reaches more than 1.6 times the minimum dynamic load strength of ISO standard.
● The products are matched with well-known escalator host manufacturers at home and abroad and are widely used in various subway stations, high-speed railway stations,s and other rail transit and shopping malls escalators, among which the reinforced main drive chain is mainly used in public transport heavy-duty escalators.
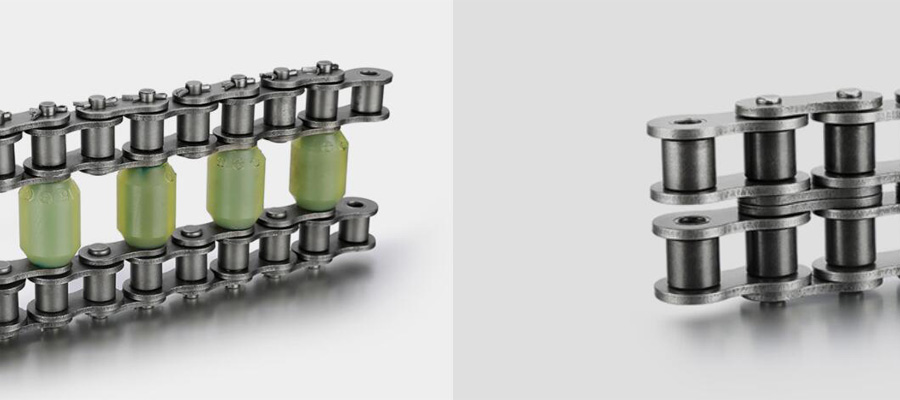
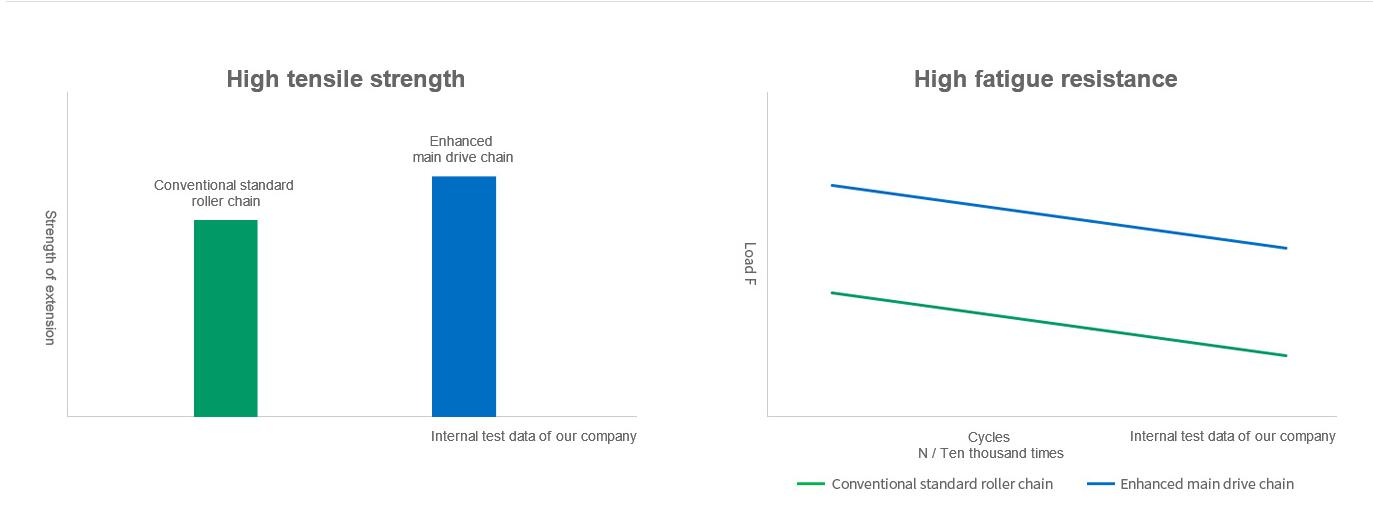
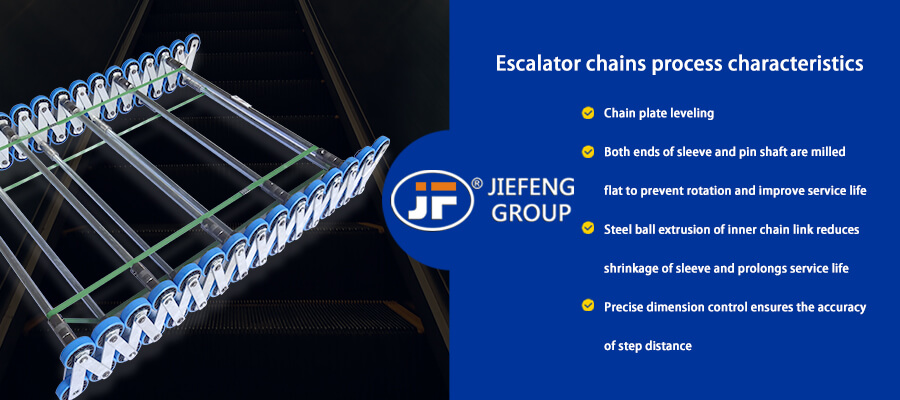
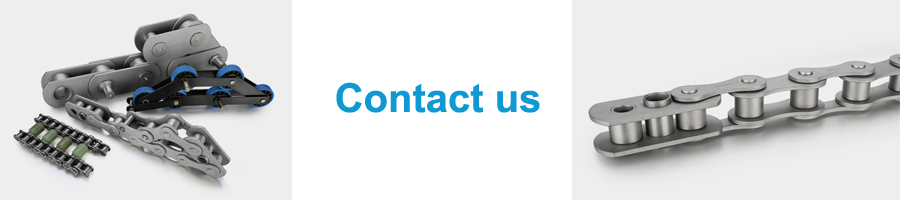
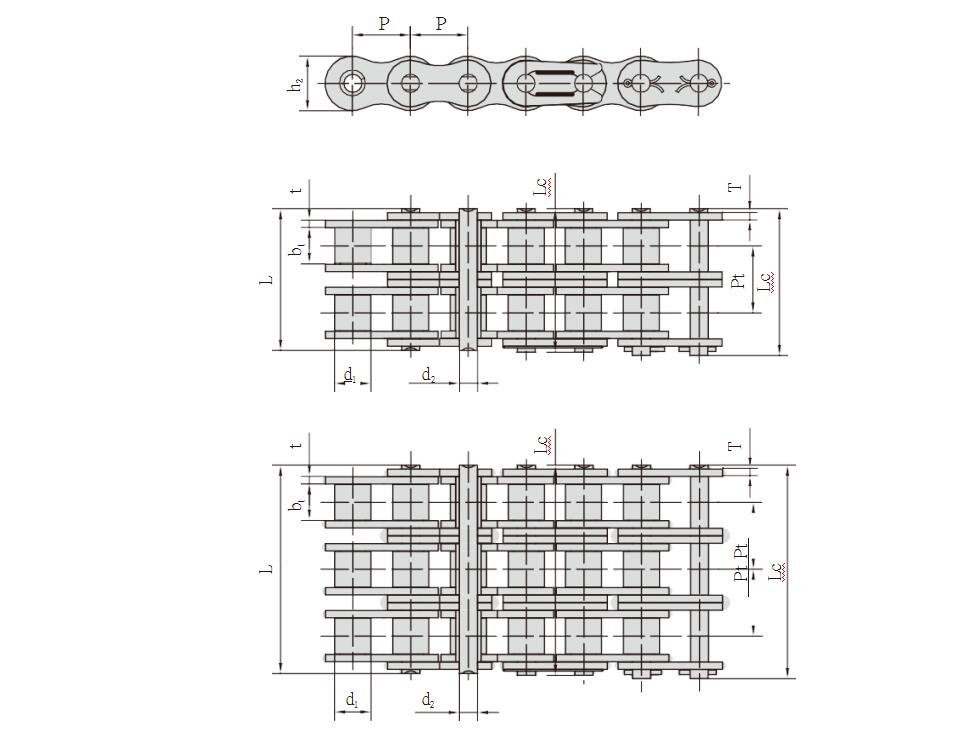
JIEFENGChain No. |
节距Pitch P mm |
滚子直径Roller diameter d1 max mm |
内节内宽Width between inner plates b1 min mm |
销轴直径Pin diameter d2 max mm |
销轴长度Pin length | 内链板高度Inner plate depth h2 max mm |
链板厚度Plate thickness t/T max mm |
排距Transverse pitch Pt mm |
抗拉强度Tensile strength Q min kN/lbf |
动载强度Dynamic load strength Fd min kN |
每米长重Weight per meter q kg/m |
|
L max mm |
Lc max mm |
|||||||||||
16A(FQ)-1 | 25.40 | 15.88 | 15.75 | 7.92 | 32.70 | 36.50 | 24.00 | 3.25 | - | 56.7/12746 | 9.55 | 2.60 |
16A(FQ)-2 | 25.40 | 15.88 | 15.75 | 7.92 | 62.70 | 65.30 | 24.00 | 3.25 | 29.29 | 113.4/25492 | 12.80 | 5.51 |
16A(FQ)-3 | 25.40 | 15.88 | 15.75 | 7.92 | 91.70 | 94.60 | 24.00 | 3.25 | 29.29 | 170.1/38238 | 19.20 | 7.89 |
16B(FQ)-1 | 25.40 | 15.88 | 17.02 | 8.28 | 36.10 | 39.10 | 21.00 | 4.15/3.10 | - | 60.0/13488 | 12.50 | 2.71 |
16B(FQ)-2 | 25.40 | 15.88 | 17.02 | 8.28 | 68.00 | 71.00 | 21.00 | 4.15/3.10 | 31.88 | 127.5/28662 | 19.00 | 5.42 |
20A(FQ)-2 | 31.75 | 19.05 | 18.90 | 9.53 | 76.40 | 80.50 | 30.00 | 4.00 | 35.76 | 174.0/39115 | 19.56 | 7.80 |
20A(FQ)-3 | 31.75 | 19.05 | 18.90 | 9.53 | 112.20 | 116.30 | 30.00 | 4.00 | 35.76 | 261.0/58673 | 29.35 | 11.77 |
20B(FQ)-1 | 31.75 | 19.05 | 19.56 | 10.19 | 41.30 | 45.00 | 26.40 | 4.50/3.50 | - | 95.0/21356 | 13.50 | 3.70 |
20B(FQ)-2 | 31.75 | 19.05 | 19.56 | 10.19 | 77.80 | 81.50 | 26.40 | 4.50/3.51 | 36.45 | 195.0/43836 | 30.00 | 7.20 |
24A(FQ)-2 | 38.10 | 22.23 | 25.22 | 11.10 | 95.80 | 99.70 | 35.70 | 4.80 | 45.44 | 284.0/63843 | 46.00 | 11.70 |
24B(FQ)-2 | 38.10 | 35.40 | 25.40 | 14.63 | 101.70 | 106.20 | 33.20 | 6.00/4.80 | 48.36 |
Selection of chain drive power
The standard of "Guidelines for the Selection of Roller Chain Drives"(GB/T 18150-2006 / ISO 10823:2004) had been issued. If you try to calculate the actual transmission power of chain, you must consider revising the transmission power of driving sprocket (input power).
Actual power(Corrected power)=input power×service factor× teeth factor Service factor is listed in the following table.
Teeth factor = (19/Zs)1.08 (Zs—tooth number of the small sprocket)
■工况系数表 Service factor table
■工况系数表 Service factor table
从动机械特性 Driven Mechanism Characteristic |
主动机械特性 Driving Mechanism Characteristic | ||
平稳运转 Smooth Running |
轻微振动 Slight Vibration |
中等振动 Medium Vibration |
|
平稳运转 Smooth Running | 1.0 | 1.1 | 1.3 |
中等振动 Medium Vibration | 1.4 | 1.5 | 1.7 |
严重振动 Severe Vibration | 1.8 | 1.9 | 2.1 |
The chain factories with long history in the world have their own chain transmission power rating graph and power diagram. We can refer to the GB/T 18150-2006 / ISO 10823:2004 standard selecting the drive power or selecting chain according to the drive power, the condition is that we should know the tooth number of the small sprocket and its speed. Only if the actual power is within the range of rating power of the power rating graph, the selected chain is suitable.
Now we use the transmission part in walking tractor and the transmission power in rotary tillage to proof whether the chain selection is correct.
■ Chain drive part
■ Chain drive part
Small sprocket speed ns=1351 r/min Tooth number of small sprocket Zs=14
Actual power (Corrected power)=10.944hp=8.16kW
From B series horsepower rating graph, you will find selected 08B-2 chain is suitable.
■ Ratar y tillage chain part
■ Ratar y tillage chain part
Small sprocket speed ns=199 r/min Tooth number of small sprocket Zs=13
Actual power (Corrected power)=9.888hp=7.37kW
From A series horsepower rating graph, you will find selected 12A-2 chain is unsuitable. You should choose 16A-1 or 60H-2 heavy duty roller chain instead of 12A-2.
■ The main characteristics of this power graph are as follows:
■ The main characteristics of this power graph are as follows:
For drive Zs=19
Chain length: 120 pitches Transmission ratio: 1 : 3 to 3 : 1 Service life of chain: 15000 hours
■ The main characteristics of this power graph are as follows:
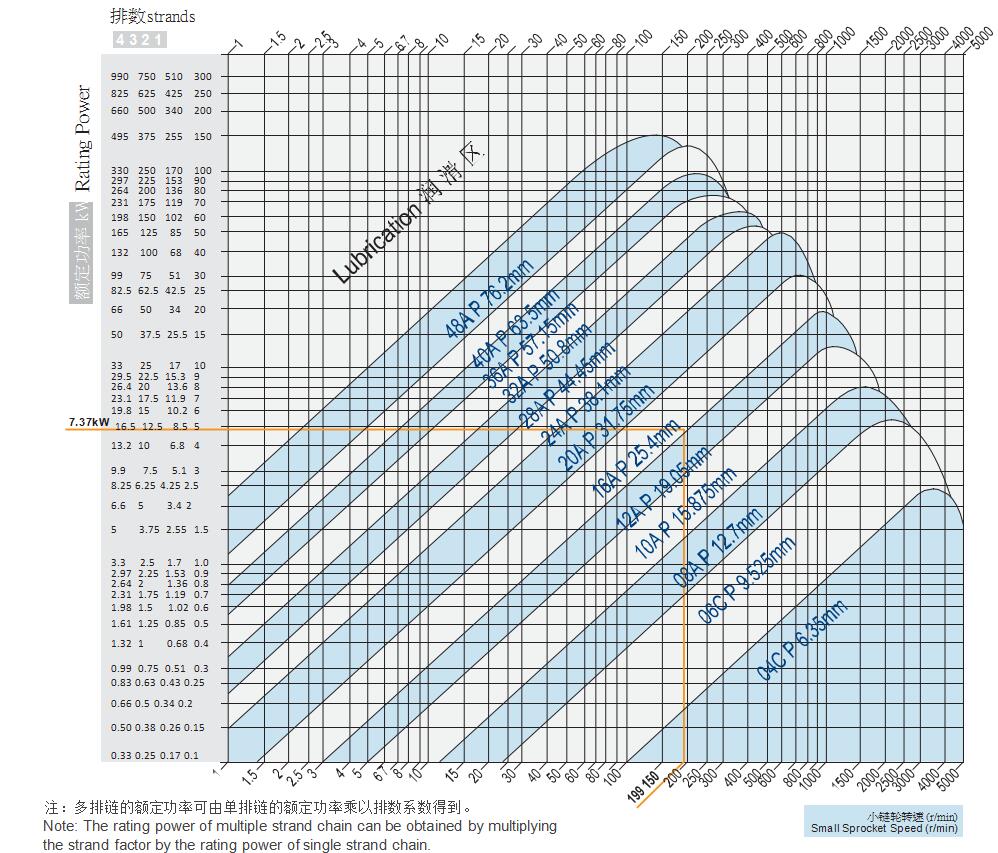
排 数 Number of strand | 1 | 2 | 3 | 4 | 5 | 6 |
系 数 Factor | 1.0 | 1.7 | 2.5 | 3.3 | 4.1 | 4.9 |
功率曲线图(B系列滚子链)
Power rating graph ( B series roller chain )■ The main characteristics of this power graph are as follows:
For drive Zs=19
Chain length: 120 pitches Transmission ratio: 1 : 3 to 3 : 1
Service life of chain: 15000 hours
Service life of chain: 15000 hours
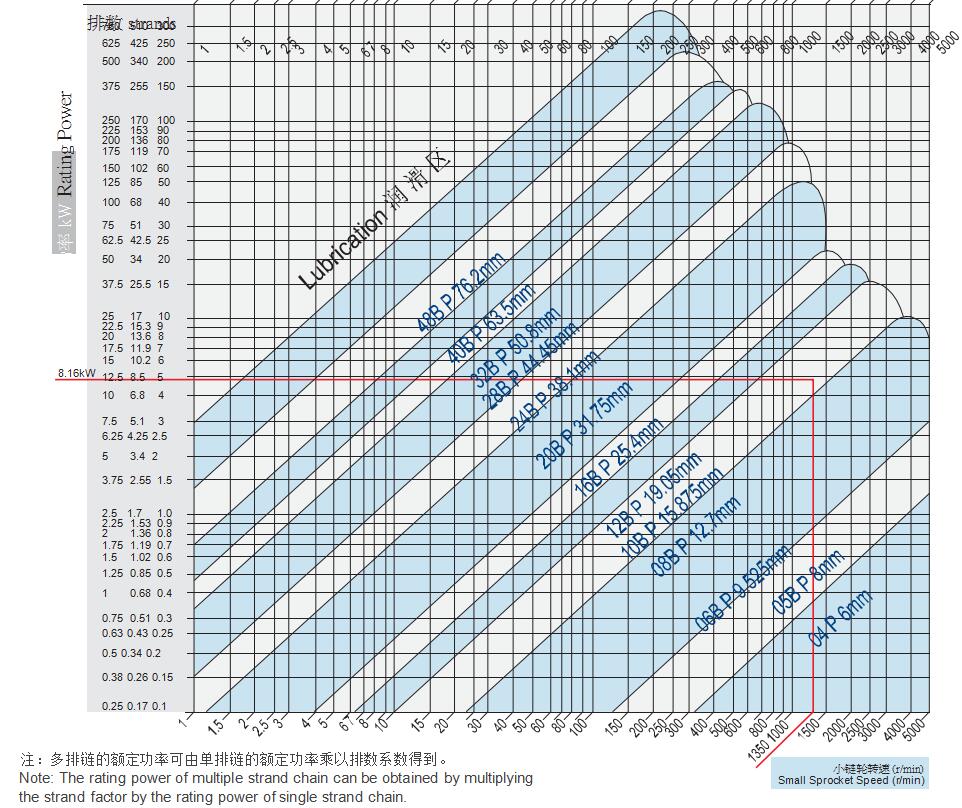
■ 排数系数表 Strand factor table
排 数 Number of strand | 1 | 2 | 3 | 4 | 5 | 6 |
系 数 Factor | 1.0 | 1.7 | 2.5 | 3.3 | 4.1 | 4.9 |
Maintenance for Roller Chain Drive
t’s very practical to illustrate the convention- al maintenance of roller chain drive because of its wide application in industry. Better maintenance, less failure. In practice, only following some simple maintenance principals, we can easily save costs and make its service life longer, and then making the operation more efficient.
t’s very practical to illustrate the convention- al maintenance of roller chain drive because of its wide application in industry. Better maintenance, less failure. In practice, only following some simple maintenance principals, we can easily save costs and make its service life longer, and then making the operation more efficient.
1.Each sprocket in the driving system should have good coplanarity and the chain path should always be smooth.
2.The sagging of chain loose side should be suitable and for the adjustable center distance level and angle drive, the sagging should be 1%~2% of the center distance. For conditions of vertical drive and under vibration load、reverse drive and dynamic brake ,the sagging should be smaller. It’s very important to check and adjust the loose side sagging frequently in the chain drive maintenance.
3.Good lubrication is also very important. Whichever lubrication method you choose, the most important thing is to make the lubricating grease distribute evenly in each chain joint clearance. If not necessary, avoid selecting big viscosity heavy oil or lubricating grease since it will jam the clearances gone to joints friction surface with dust after a period of time. Periodi- cally clean the roller chain and check its lubrication condition frequently. Disassembly the pin and bush, if necessary. If the friction surface is brown or dust color, it may be caused by insufficient lubrication.
4.Chains and sprockets should be always in good condition.
5.Frequently check the working surface of sprocket teeth ,adjust or replace it when it’s excessively worn.
Troubleshooting Instructions
Troubleshooting Instructions
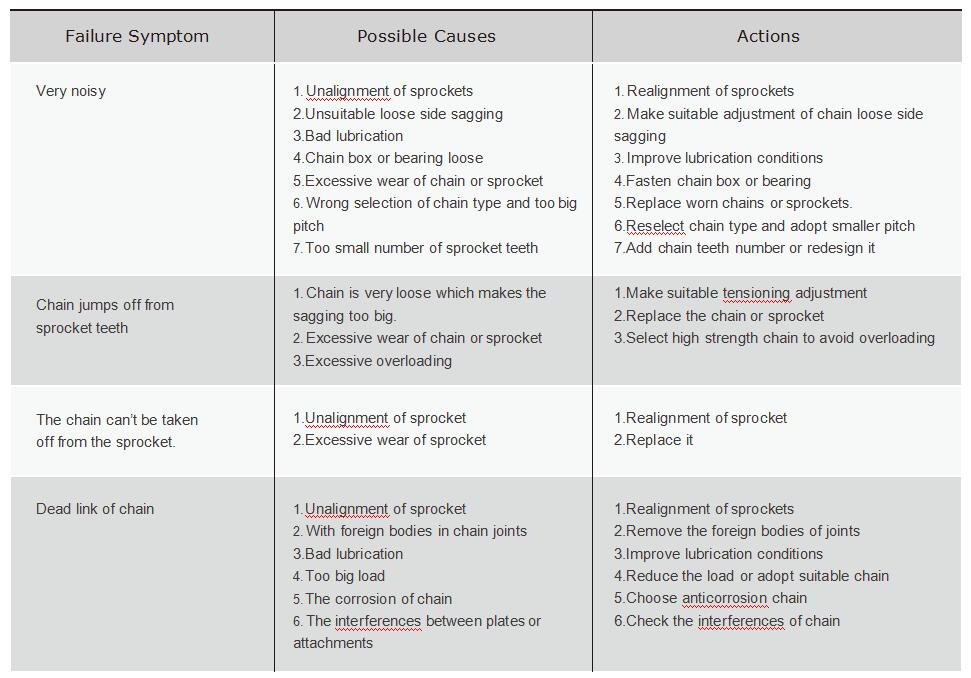
Failure Symptom | Possible Causes | Actions |
Roller cracked or deformed |
1. Too big chain pitch or too small number of sprocket teeth 2. Sprocket teeth have foreign bodies. 3.The chain climbs onto sprocket teeth too high. 4.Excessive chain impact load |
1. Select small pitch chain or add sprocket teeth number 2. Remove all the foreign bodies or replace chain 3.Replace the chain and make appropriate tensioning 4.Reduce the impact of chain |
Pin rotates or plate hole drawn long |
1.Chain overloaded |
1.Eliminate the overloading causes or adopt large specification chain |
Pin broken or plate broken along the hole connecting line direction |
1.Excessive overloading |
1.Eliminate the overloading causes or adopt large specification or higher strength chain; if sprocket failure symptom found, replace it |
Plates broken![]() |
1.The load above chain dynamic capacity |
1.Selecting big pitch chain or reduce dynamic load |
Excessive side-wear of plates or sprocket teeth |
1. Sprocket not coplanar or ending beat severely 2. Bad bearing stiffness of sprocket 3.Severe twist of chain |
1.Increase machining and installation precision 2.Increase bearing parts stiffness 3.Replace chain |
Outer link outside rubbed |
1. Chain not tensioned and jump, then to hit adjacent bodies 2. Chain box deformed or with foreign bodies inside |
1.Make appropriate chain tensioning 2.Eliminate chain box deformation and remove foreign bodies |
Pin worn or bush bonded with pin |
1. Bad lubrication 2. Chain speed too high or chain overloaded |
1.Supply suitable lubrication system 2.Lower the speed or reduce the load |
Excessive wear of sprocket |
1. Bad lubrication 2. Inferior material of sprocket and insuffi- cient teeth surface hardness |
1.Improve lubrication conditions 2.Improve sprocket material quality and its teeth surface hardness |
Locking parts such as spring clip and cotter pin etc. become loose. |
1.Chain wobbling heavily 2.Knock with obstructions 3.Locking parts wrong installed |
1. Make suitable tensioning or consider adding supporting board for guide plate 2. Remove all obstructions 3. Improve the installation quality of locking parts |